Strict product quality control system Professional customer service system
Technical Advantages
ADVANTAGES OF UV LED TECHNOLOGY
Invention patent - COB packaging technology
COB packaging technology is to fix the LED chip on a high thermal conductivity metal substrate or ceramic substrate, and build thermal resistance through the direct heat dissipation of the substrate, which has a good heat dissipation effect; the UV LED light source packaged by COB has a relatively high radiation flux/area. It greatly improves the optical density and achieves high radiant flux output in a small light-emitting area, which can greatly meet the market demand for high optical power density.
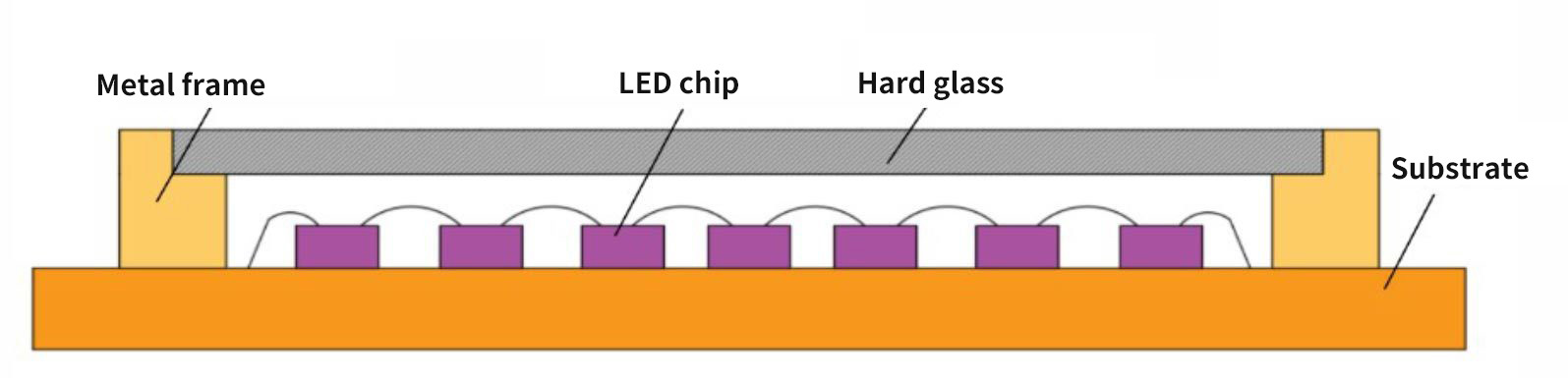
Inorganic packaging technology
The UV LED inorganic packaging device is characterized in that it includes a ceramic bracket, metal, and a quartz/sapphire light window. The ceramic bracket is bonded to the quartz/sapphire light window by laser sealing and welding technology, and a closed air cavity is formed between the UV LED chip and the bracket. , the water vapor and magazines in the outside air next door corrode the internal chip, which greatly improves the life, performance and reliability of the device.
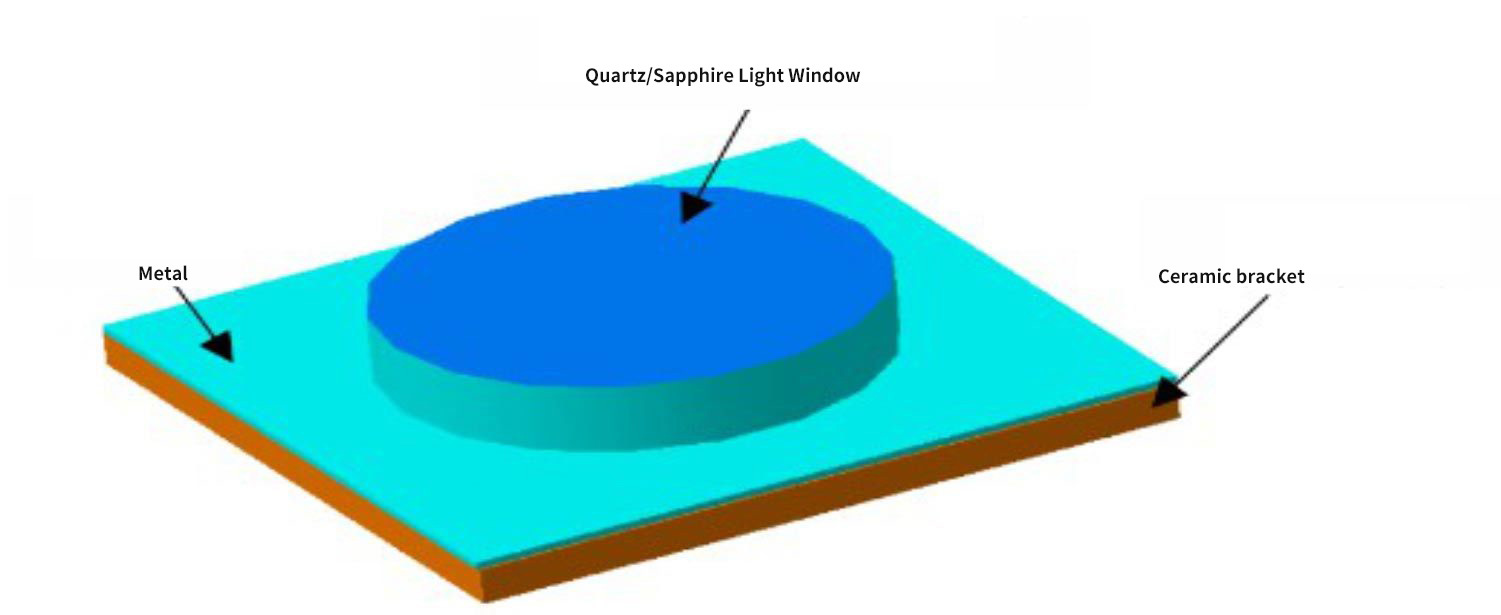
Eutectic welding technology
Eutectic welding is a low melting point alloy welding. The LED chip is fused on the copper-clad and gold-plated substrate through eutectic welding, and the thermal and mechanical properties of the LED device are greatly improved through metal connection.
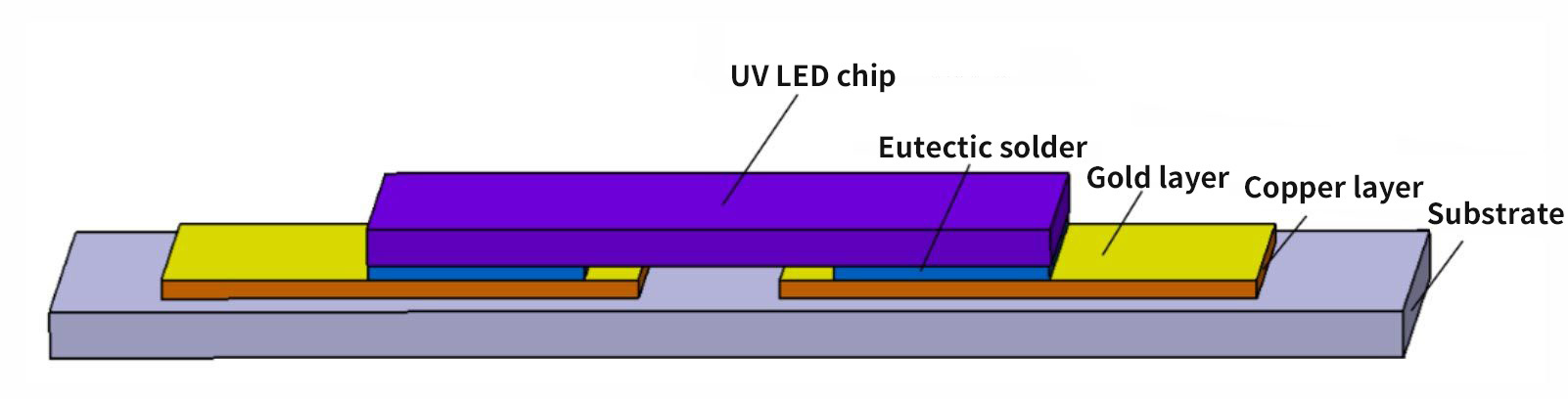
COB LED TECHNOLOGY ADVANTAGES
Efficient COB LED light source production system guarantees strict color control standards
100% strict light splitting, good light control effect, high color consistency of multiple batches of the same bin number, set bin numbers in strict accordance with the corresponding American standard and European standard standard system, the main file meets the 2-3 step color tolerance requirements
In order to meet the color control standards, the company strictly controls the process from raw material selection to production point powder:
1. Stable supply of raw materials:
Reached a long-term cooperation consensus with major chip suppliers, and selected the same chip band for the same color temperature.
2. Real-time monitoring of powder production process:
The phosphor powder is automatically mixed with the automatic powder mixing machine, which avoids the errors that are easy to occur in manual powder mixing.
During the powder ordering process, real-time monitoring is performed while ordering powder, which can achieve meticulous control over the powder ordering process.
3. Taking the remote photoelectric test equipment as the standard machine, it has a complete calibration system, and performs regular calibration on all photoelectric test equipment to ensure the accuracy and consistency of photoelectric parameters.


Strict product quality control system
The complicated inspection system ensures product quality, and the entire manufacturing process involves up to 247 inspection items:
1. There are 52 incoming inspection items, which are divided into substrates, chips, die-bonding adhesives, dam adhesives, encapsulation adhesives, phosphors, solder pastes, gold wires and other raw materials;
2. There are 160 inspection items in the first half of the light source production process, which are divided into laser marking, die bonding, wire bonding, testing, dam enclosure, powder spotting and other processes;
3. There are a total of 31 inspection items in the second half of the light source production process, which are divided into processes such as light separation, material breaking, appearance, loading inspection, warehouse warehousing and warehouse delivery;
4. There are 4 routine routine tests.